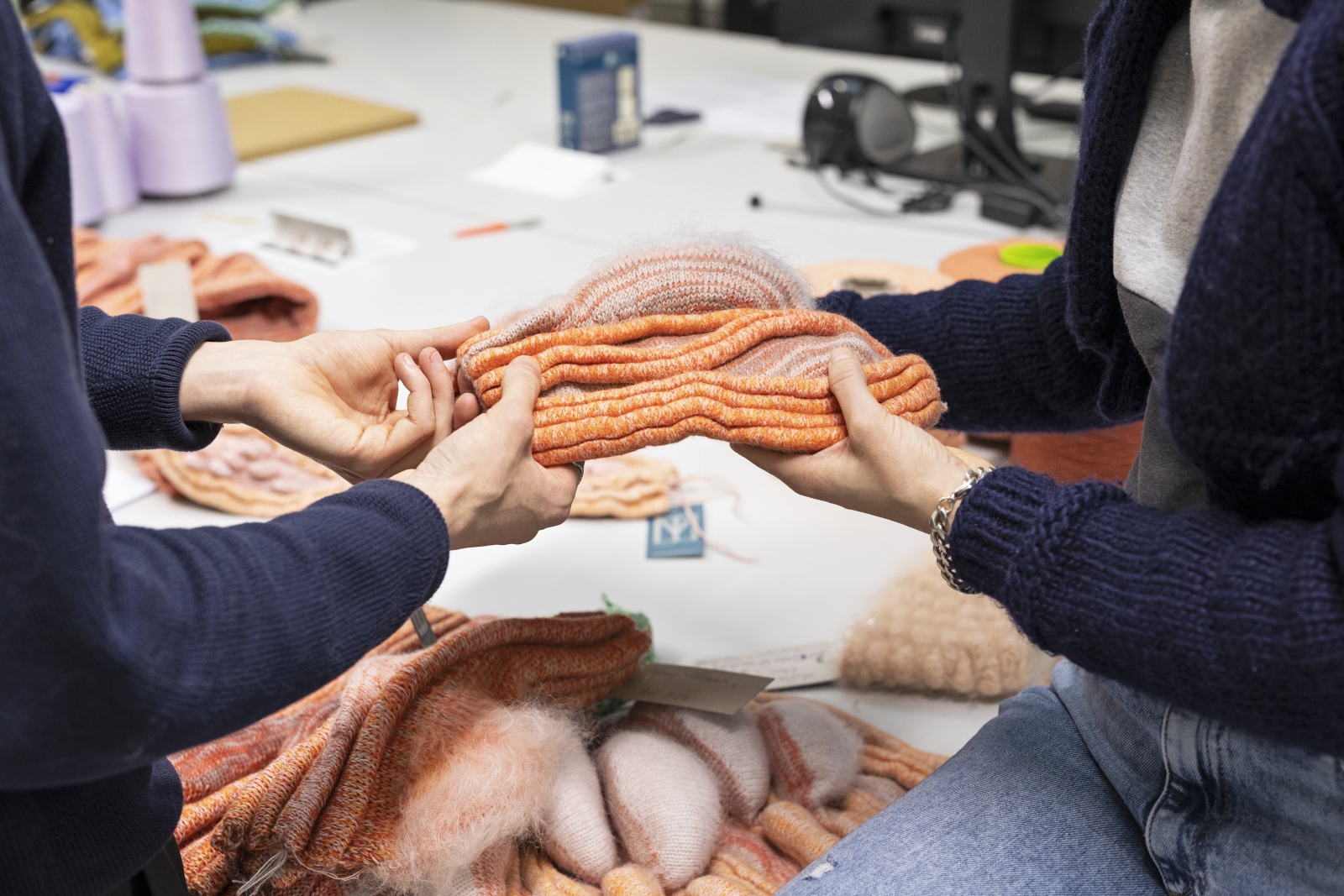
'3D printing' with the new knitting machine
2 January 2024
Making sustainable three-dimensional shapes from textiles, that is our New Year's wish. Our very latest knitting machine was specially purchased because it can knit 3D shapes even better. In the TextielLab, an ambitious research project on so-called fully fashioned knitting has started.
We started 2024 with a resolution: We want to raise the profile of knitting in the visual arts by pushing the boundaries of the technique. “Historically, weaving has been a bigger part of our DNA,” says Noortje van den Elzen, project leader of the Research & Development (R&D) programme. This is why weavers have tended to take the lead in pioneering experiments in the lab. But the past year has seen the knitting department catching up fast.
Ada M. Patterson's work 'Dark Enough to see the Stars' made on the knitting machine. Photo: Patty van den Elshout | Sofie Roterman inspects her samples in the TextielLab. Photo: Patty van den Elshout
New additions
This catch-up started with an investment in people and machines in the knitting department. This included the purchase of a fully digitally adjustable circular knitting machine that can handle thicker yarn, greatly increasing the possibilities of circular knitting. The machine is mainly used in the industry for making mattresses, but product developer Mathilde Vandenbussche and technical specialist Yani Chuang are extensively testing it for other uses. In the meantime, the circular and flat knitting experts have introduced each other to ‘their’ machines, to enable more cross-pollination between the techniques. Last month, the latest acquisition was eagerly awaited: the STOLL CMS 830 ki S knit & wear E7.2. Quite a mouthful, so we call it the S-machine for short.
3D printer vs knitting machine
The new machine, which was installed in the lab just before Christmas, is ideally suited for so-called fully fashioned knitting. This is where seamless 3D shapes are knitted on the machine, rather than created out of individual components, often eliminating the need for assembly. “Basically, everything you can 3D print, you can knit, but with the quality and refinement of textiles,” says Van den Elzen. “We think that’s an interesting starting point for makers, even if they have never knitted in their lives.” The beauty of the S-machine is that it allows us to knit even more distinct shapes than current knitting machines, as we can make longer differences and larger protrusions.
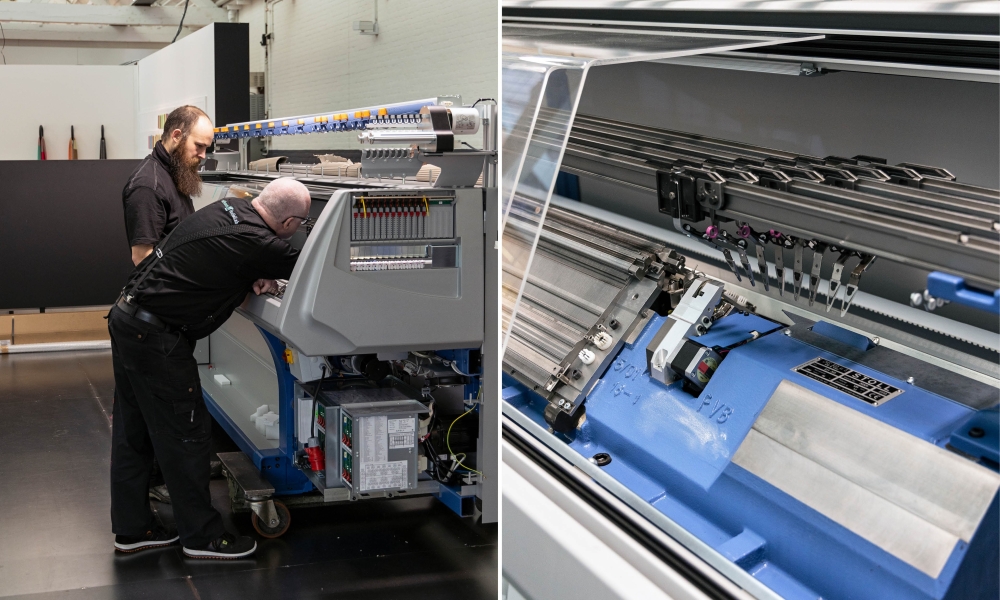
The S-machine gets installed in the TextielLab. Photos Josefina Eikenaar
Pushing boundaries
Our knitting experts are eager to start experimenting. “We’ve noticed an increasing demand for fully fashioned knitting from makers,” says Van den Elzen, “but it’s also an area we want to grow in ourselves.” So we won't just get started by ourselves, but enlist the help of three artists: Elmo Mistiaen, Marlou Breuls, and Henrik Vibskov. All three of them will work on an R&D assignment this year to explore the possibilities of the S-machine together with our product developers and technicians. We hope that the artists' requests will additionally challenge both the product developers and the machines. The teams assembled for this purpose will each be given no less than 40 development days in the lab allowing them to delve into their research and be able to create a large object.
Product developer Sarena Huizinga and Elmo Mistiaen at work in the lab. Photos:Josefina Eikenaar
Voluminous body art
In this research project, we do not stop at experiments and interesting small-scale samples "With this programme, we really make time and space for knitting," says Van den Elzen. The aim is to arrive at an extensive 3D knitted object: “We want to make something spectacular.” The results will be shown at the end of this year in a new exhibition that is all about volume. The first two artists have been commissioned to make a voluminous and sculptural body piece. The piece can, but doesn’t have to be, a wearable fashion item. However, it must add to the current discussion about body shaming, body positivity, sustainability and developments related to the manipulated body. First up is the Belgian artist Elmo Mistiaen, who uses artificial intelligence to design his ‘biomorphic outdoor fashion & weird design’.
“Everything you can 3D print, you can knit.”
- Noortje van den Elzen
Sustainable samples
Mistiaen has been paired with product developer Sarena Huizinga for this project, and the two will start exploring the limits of the new machine this month. A key focus is the use of sustainable yarns, such as Dutch wool and post-consumer recycled yarn from the Tilburg-based company Wolkat. One of the goals of the R&D programme is to develop a series of sustainable samples and add them to the Sample Studio. “These examples give other designers a flying start, because the research has already been done and the technical specifications of the yarns are available,” explains Van den Elzen. “By making sustainable yarns visible and tangible in finished samples, it’s much more likely that other people will start working with them.”
So be sure to stop by the TextielLabs knitting department during your next visit to the museum. You might just bump into one of the artists there and witness the latest knitting breakthrough!